Now that you are done implementing the preventive maintenance plan in your company, the question is: do you know how to identify if the strategy is working or failing? Can you also tell the management that your work is beneficial for them?
As the owner of a small business, you know that preventive maintenance (PM) is important for reducing downtime and increasing productivity. Even so, the preventive maintenance schedule you’re currently using isn’t quite up to par, and you should give your whole system a thorough look.
This article will show you how to use a few key metrics to measure how well preventive maintenance works.
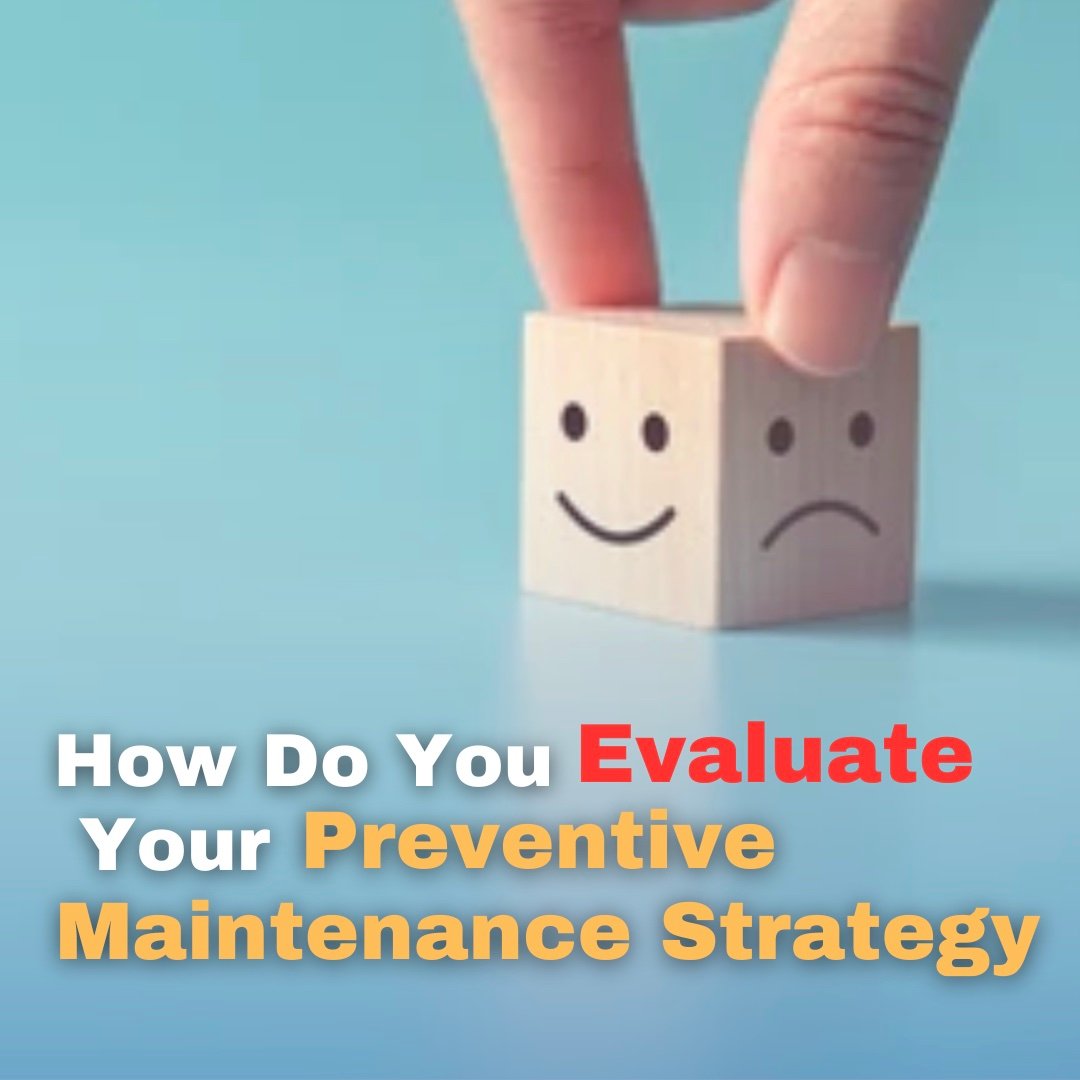
Evaluating the Effectiveness of the Preventive Maintenance Strategy
Performing a preventative maintenance program evaluation makes a lot of sense. If there are things you want to change in the current practices, you should first evaluate those. Because of your assessment, you can analyze the program’s weaknesses.
Your main job is to look for and analyze any weaknesses in the program before you change how things are done now. In order to achieve this, both you (the owner) and your management team must be deeply involved in the process.
You can use three performance indicators to measure the efficiency of your planned preventive maintenance. The planned maintenance, preventive maintenance compliance, and critical scheduling percentages can determine if you are succeeding or not in your strategy. We will find out and evaluate what is happening to ensure that your planned preventive system is working.
Planned Maintenance Percentage
A planned maintenance percentage (PMP) measures the number of planned maintenance tasks against the completed maintenance tasks. The value of this indicator is significant for deciding what should be changed or fixed in the company. The possible effects of this indicator are on maintenance scheduling, resource allocation, and maintenance processing.
You don’t need to be a math genius to calculate the planned maintenance percentage. To determine the time spent on planned preventive maintenance, divide the hours spent on maintenance (including reactive maintenance). For the formula, here it is:
For a preventive maintenance example:
The Water Utility
A water utility company spent 1,300 hours on maintenance during the first quarter of 2023. Of the 1,300 hours, 1000 hours went into planned maintenance tasks.
PMP = 1000 ÷ 1,300 = 0.769
= 0.769 x 100
= 76.9%
If the percentage of planned maintenance is less than 85 percent, your company needs to conduct additional inspections, and there may even be a need to make an emergency trip. What is the possible reason why it happens?
Preventive maintenance is lacking
When your planned maintenance percentage falls below 85%, you spend at least 15% of your time on reactive maintenance. Basically, 15 percent of your maintenance technicians’ time is spent fixing faults that could have been avoided.
Preventive Maintenance Compliance
The preventive maintenance compliance KPI measures how well a PM schedule is followed. The exact method of calculating it will be discussed later, but it tells manufacturers how many tasks have been completed out of the total number.
It is also crucial that you know that PMC serves as an indicator that will help you understand your PM strategy’s flaws. So let’s find out how the PMC is computed and what its limit is as a metric.
We can assure you that you will always be able to calculate PMC. All you need to do is first find the total number of completed PM tasks over a certain period. Then divide the total number of completed tasks by the number of scheduled tasks. When you’re done computing, multiply the answer you got by 100. The answer you get is your PMC.
Always remember that the scheduled PM tasks only count here. Reactive maintenance tasks or unplanned PM tasks are not included in this formula.
For preventive maintenance example:
Consider a scenario in which 95 tasks were scheduled over 30 days, and 70 of them were completed. 70 ÷ 95 = ~0,74, which equals a PMC of 74%.
The preventive maintenance plan compliance rate should be 90% to reduce downtime and unnecessary maintenance and repair costs. In the case of non-compliance with the maintenance plan, the following may be the reason:
The technology you are using isn’t right
A preventive maintenance plan will only work if you have the right tools. Can you imagine that the person who cut your hair at the haircut salon suddenly stopped and said that he used the wrong razor on your hair, then he took the right one from his bag? Excel sheets have been a massive improvement over paper sheets, but they don’t send reminders, track equipment malfunctions, or facilitate communication between teams.
Scheduled Maintenance Critical Percent
This metric measures the impact of late planned maintenance work on the Scheduled Maintenance Critical Percentage (SMCP). It helps you prioritize which preventive maintenance jobs to complete by quantifying the risk associated with overdue preventive maintenance tasks.
To figure out SMCP, you need to know how often the PM work order is done and how long it takes. The formula below can be used once you have this information:
Here’s the preventive maintenance example.
An asset’s bearings must be lubricated every 15 days, but you’re five days behind schedule. In addition, you should replace the motor on the same piece of equipment every 90 days. A work order has been late for seven days. The only thing you need to accomplish today is one of these tasks. You can choose the most critical one with the help of SMCP:
- Lubricating the bearings as PM1: (5+15) ÷ 15 x 100 = 133%
- Replacing the motor as PM2: (7+90) ÷ 90 x 100 = 108%
Based on the results of the calculation, it is shown that lubrication should be done first rather than replacing the motor.
As much as possible, the company’s scheduled maintenance percentage should be low. The delay between tasks should be 0 to get a percentage of 100. But if you don’t follow through on many tasks. Maybe you are:
Weighing tasks poorly
Tasks with a high SMCP frequently take longer than expected, or there aren’t enough technicians. To increase your SMCP, you should spend more time and money on the tasks that have the highest SMCP.
Poor priority setting
Any task that significantly impacts your operation should be reconsidered if it is continually left undone after its due date. Ensure your highest priority tasks are at the top rather than burying them under a half-dozen less critical tasks.
In addition to helping you measure your maintenance plan’s effectiveness, this indicator will allow you to determine what factors affect your company’s success.
Final Thought
When implementing preventive maintenance, you should not just leave it alone. Your strategy will be useless if the problem is at work. So you should know these important indicators to ensure that the planned tasks are done in a timely and orderly manner.
Since you already know the correct evaluation method, you can try it now in preventive maintenance. Enjoy the benefits you will get afterward!
Interesting Related Article: “5 Best Small Business Promotional Items“